管道内检测器是一种集成了检测、信息采集、处理、存储等技术的装置,其技术水平一定程度上代表了一个国家的工业发展水平。目前,中国内检测技术在原理应用、精度等方面与国外仍存在一定差距。针对中国管道环焊缝缺陷、类裂纹缺陷以及针孔小缺陷检测能力不足和识别率不高的难题,研发了新一代超高清亚毫米级管道漏磁内检测器。通过磁路仿真设计、探头开发、海量数据采集和存储,建立基于深度学习的BP神经网络模型,提高了超高清检测技术的缺陷量化和识别能力,对推动中国管道内检测技术发展与工业化意义重大。
关键技术:
磁路有限元数值仿真
以管径323mm的管道为例,分别计算壁厚为6.4mm、8.0mm、9.5mm、10.3mm、12.7mm时管道外壁的漏磁场强度。基于磁场分析的有限元仿真方法,建立超高清管道漏磁检测系统的有限元仿真模型,计算出管壁外部2mm提离时的磁场强度,为管道漏磁检测系统的开发提供参考。
亚毫米级间距探头研制
成功研制出T字形亚毫米级间距霍尔探头,实现单个探头各通道间距达0.6mm。相较于现有技术的单排设计,此设计方式布置的探头个数明显增多,排布更加紧凑,相邻两个探头的间隙达到最小,有助于检测出管道内部针孔型小缺陷,大幅度提高检测精度。同时,相邻的两个探头沿检测器中心轴的径向保留一定距离,保证检测器在管道内运行时,探头具有一定的活动空间,减少因管道壁的挤压对探测机构造成的损坏。
数据分析软件开发与数据集构建
01 数据采集
数据采集系统的硬件主要包含A/D采样芯片、现场可编程逻辑门阵列、双口RAM处理器缓存、ARM控制器、NANDFlash存储器。对于不同类型的检测信号,其数据采集方式不同,非磁检测信号的数据量小,经信号调理后,直接送入ARM处理器模数转换端口进行采集,而漏磁检测信号数据量大,主要由FPGA控制A/D转换芯片实现多路采集。
02 数据分析软件开发
对于超高清亚毫米级检测技术,海量数据的读取和分析是关键,开发了一套数据分析软件,实现漏磁数据、变形数据以及IMU数据的统一整合与分析。数据分析软件采用统一基准利用缺陷特征参数进行缺陷长度、宽度、深度的量化,可进行管道缺陷特征自动辨识和缺陷量化,同时具备灵活的统计、报表及输出功能,生成三维管道缺陷点分布,辅助完成缺陷自动化、智能化识别,并能实现缺陷等效尺寸的计算和临界破坏压力值的分析,实现对缺陷点安全性的评估。
03 检测数据比较
新一代超高清内检测数据信号与第4代三轴高清数据信号、第3代高清数据信号相比,在数据密集程度、缺陷像素质量等方面获得大幅提高。以323mm管道内检测器为例,第3代内检测器采用单轴传感器布设,漏磁通道数量为80个,内外部缺陷识别通道30个;第4代内检测器采用三轴模拟霍尔传感器3.0~6.9mm布设,漏磁通道360个,IDOD通道30个,轴向采样间距2mm;新一代超高清内检测器采用三轴亚毫米数字霍尔传感器布设,漏磁通道768个,IDOD通道768个,轴向采样间距1mm,总通道数1536个,数据显示的密集度大幅增加。
04 管件高清数据库建立
为了更好地识别管道附属设施,建立了管件基础数据库,表征信号特征,实现了管件特征的自动识别与分析,提高了管件智能化识别判断的准确性。
05 缺陷数据库建立
基于SQL Server建立关系型数据库,定期存储海量管道内检测缺陷图像,采用B/S的架构模式,建立.NET框架和C#语言为开发工具的交互界面,界面通过.NET框架实现与数据库之间的交互,数据库可设定缺陷类型选项,基于聚类算法实现显示标签特征的缺陷数据集。
缺陷智能化识别
采用BP神经网络对管道缺陷当量尺寸进行量化分析,选择有效的特征量作为BP网络输入层。以缺陷深度的量化为例,其漏磁信号特征量采用轴向分量的峰面积S1和峰值P1以及径向分量的峰面积S2和峰值P2共4个特征量作为BP神经网络的输入层,建立一个包含上述4个输入单元的输入层,包含8个单元的隐含层和包含缺陷深度1个输出单元的输出层的缺陷深度回归预测BP神经网络。
对比训练集、测试集的真实值与预测值可知:训练集与测试集的决定系数均为0.999,对于缺陷深度具有较好的预测;图中真实值和预测值大部分重合度较高,预测值与真实值十分接近,证明此预测模型具有相当高的可靠性。
工程应用案例
2020年2月,新一代超高清亚毫米级管道内检测设备在中石化某输油管道进行了应用。该管道全长105.5km,常规壁厚6.4mm,管道直径323mm,设计压力9.5MPa。该设备拥有双通道,三轴主、副探头共1536个检测通道,探头通道数量是第4代设备的5~6倍;探头间距为0.6mm,轴向采样间距为1mm,可精准描述管道焊缝缺陷,对于针眼小孔腐蚀的检测发现具有重要意义。
通过检测和开挖验证,可清晰地判断出环焊缝缺陷的异常等级和焊缝缺陷类别。开挖验证缺陷为焊缝边缘余高未填满,同时可以检测出针孔缺陷,以及其他特征(如凹陷等),缺陷检测与识别精度大幅提高。
通过开挖验证比较分析,检测器的性能指标与开挖验证检测技术指标吻合,此次检测可信度达到90%,优于80%的预定指标;可检测率达到95%以上,优于90%的预定指标;缺陷识别率达到98%以上,优于90%的检测指标。
结论与建议
1.突破了超高清漏磁亚毫米级探头间距难题,将探头通道数量增加了5~6倍,采集数据量增加15倍,实现亚毫米级通道间距的海量数据采集,基本做到缺陷的精细化描述,解决了油气管道针眼小面积深度腐蚀的难题。
2.形成了管道超高清漏磁检测、变形检测、位置检测三位一体的复合检测技术,并在同一时间轴上进行对齐和分析,定位更加准确,可以准确描述几何变形、金属损失的复合缺陷。
3.突破了管道厚壁管磁化的检测难题,将磁场强度提高到了原来的2~3倍,初步实现了管道小缺陷和环焊缝缺陷的精准检测;突破了基于海量数据的综合分析技术,大大增强焊缝的可识别性;通过与开挖数据比对分析,大幅提高焊缝未焊透、未熔合、开口裂纹等缺陷的识别精准度,基本实现焊缝的量化评价。
4.开发了基于深度学习的智能化内检测数据分析软件,建立深度学习的BP神经网络模型,实现了缺陷一体化、智能化识别,提高了小孔腐蚀的可检测能力,可有效识别面积小于1A×1A的缺陷,初步解决了当前三轴高清漏磁内检测器针对小孔腐蚀缺陷和环焊缝缺陷无法实现精确描述和量化的突出问题。
5.不断丰富超高清数据库的缺陷数量,提高软件智能化分析识别能力,在环焊缝量化评价上进一步提高精度。加大管道内检测新技术的研发,针对现有漏磁场不能检测的小渗漏、小孔泄漏等,采用声磁融合理论,开展新型内检测技术的研究。
素材来源于网络,如有侵权请联系删除。
网址:www.zkpipe.com
扫码微信直接咨询
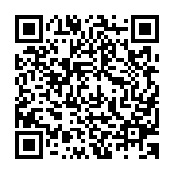