油气管道在服役过程中,由于腐蚀、机械损伤以及其他外力因素,会导致管道发生失效,甚至引起爆炸。在众多管道失效因素中,管道类裂纹缺陷是管道失效的主要因素。管道内检测是发现裂纹缺陷、消除潜在事故隐患的有效手段。电磁涡流技术具有无需与管体接触、无需介质耦合以及对表面缺陷识别能力强等优点,是目前解决类裂纹缺陷检测问题的重要探索技术之一。涡流检测技术发展迅猛,国内外各种类型的涡流仪器相继出现。
·涡流检测原理
涡流检测是一种无损检测方法,其通过测定被检工件内感生涡流的变化而引起的检测线圈阻抗的变化,既可无损评定导电材料及其工件的性能,也可发现被检工件表面、近表面缺陷。当通有交变电流的检测线圈靠近被测物体时,由于激励磁场的作用,被测物体中将感应出涡流。涡流的幅值、相位、路径均受到被测物体各项性质的影响,而由被测物体中的涡流产生的磁场也将在检测线圈中感应出电压。因此,通过对比检测线圈上感应电压的变化,即可判断被测物体是否存在缺陷。
·阻抗分析法
阻抗分析法是以分析涡流效应引起线圈阻抗变化及其相位变化之间的密切关系为基础,鉴别各影响因素效应的一种分析方法。
从电磁波传播的角度,该方法实质上是根据信号有不同相位延迟的原理来区别工件中的不连续性。
从矢量分析的角度,涡流检测获得的检测信号可以看作是缺陷、干扰以及正常的工件对线圈的多种阻抗影响信号的叠加,是各种影响信号单独作用时对线圈阻抗影响信号的矢量总和。
因此,可以对探头线圈施加多个频率叠加的激励信号,然后将获得的检测信号通过矢量运算,能够获得缺陷信号,同时抑制干扰,实现缺陷检测。
·高速自动涡流检测试验装置
为了模拟管道内检测的工况条件,自主设计并搭建了高速自动涡流检测试验装置(如下图),其主要包括自动检测模块、探头驱动模块、信号提取模块及信号采集模块。自动检测模块主要功能是固定缺陷试件、夹持涡流探头,通过触摸屏控制实现对管道缺陷试件的自动/手动状态的定速(速度为0~4.8m/s)检测。探头驱动模块由直接数字合成电路、放大电路组成。信号提取模块由正交矢量锁相放大电路实现,提取探头信号中的幅值与相位信息。信号采集模块采用基于FPGA的高速信号采集系统,使用FPGA驱动并行AD芯片对锁相放大器的输出信号进行采集,并对采集数据进行预处理,剔除误码,对数据进行打包,通过USB端口传入电脑进行数据处理。
油气管道类裂纹缺陷涡流内检测试验装置组成示意图
·试验条件及参数设置
试验所用探头为绝对式涡流检测探头,选用管径为813mm、壁厚为14mm的X65钢级管道切片,加工制作了2组缺陷试件(如下图)。其中,第1组缺陷是采用高频疲劳振动方法加工的真实类裂纹缺陷,第2组缺陷是采用线切割方法加工的标准类裂纹缺陷。
油气管道类裂纹缺陷涡流内检测试件参数
基本参数设置:检测试验中激励频率为100kHz,检测速度为0.8m/s,提离值为0。当分析检测速度的影响时,选用了0.8m/s、1.6m/s两种检测速度进行对比;当分析提离值的影响时,选用了0、1mm、2mm、3mm、4mm及5mm提离值进行对比分析。
试验结果
·涡流检测信号解析
试验探头采用正弦波作为激励信号产生感应涡流, 输出信号是探头阻抗与探头串联电阻对输入信号的分压。信号提取模块可以提取探头信号中的幅值、相位信息,同相输出信号、正交输出信号能够直接表征缺陷信息和探头阻抗信息,其计算式分别为:
式中,UI为同相输出信号;UQ为正交输出信号;UA为输出信号幅值;UC为探头激励信号幅值;φ为探头激励信号与输入信号相位差。
将UI、UQ作为坐标代入极坐标中,可以得到极坐标幅值U、极坐标旋转角θ,其计算式分别为:
经过滤波后的探头输出信号与激励信号的幅值、相位不同,当检测中发现缺陷时,探头输出信号的幅值、相位都会发生变化。因此,测量探头输出信号的幅值、相位变化,就可以获取探头电阻抗变化量。
·类裂纹缺陷的可识别性
选取管道本体、环焊缝处的类裂纹缺陷进行检测,并提取缺陷信号,从阻抗平面图、阻抗信号曲线两个角度分析类裂纹缺陷的可识别性。管体类裂纹、环焊缝类裂纹、无缺陷环焊缝的阻抗平面图分别具有不同的特征(如下图)。可见,位于第二、四象限的线形特征分别表征类裂纹缺陷、环焊缝,通过阻抗平面图可以明显地识别出不同位置的类裂纹缺陷。
管体类裂纹、环焊缝类裂纹、无缺陷环焊缝阻抗对比图
由于无缺陷环焊缝存在余高的影响,管体类裂纹、环焊缝类裂纹的阻抗信号曲线也存在明显的区别(如下图)。可见,阻抗信号曲线具有明显的表征类裂纹、环焊缝的特征,可以区分不同位置的类裂纹缺陷。
缺陷深度80%wt的管体类裂纹阻抗信号曲线
缺陷深度80%wt的环焊缝类裂纹阻抗信号曲线
·缺陷深度对检测信号的影响
分别选取不同缺陷深度的管体类裂纹、环焊缝类裂纹进行检测试验,由于疲劳加工与线切割缺陷的检测信号结果相同,故均以线切割缺陷为例进行分析。检测试验结果表明:不同缺陷深度的管体类裂纹的阻抗图表现为第二象限的线形特征(如下图),不同缺陷深度的环焊缝类裂纹的阻抗图特征则由位于第二象限表征类裂纹的线形特征与位于第四象限表征环焊缝的线形特征组成(如下图)。同时,随着类裂纹缺陷深度增大,管体类裂纹、环焊缝类裂纹的信号特征表现越明显。
不同缺陷深度下环焊缝类裂纹阻抗对比图
·检测速度对检测信号的影响
利用高速自动涡流检测试验装置,设定不同的检测速度对缺陷深度为50%wt的管体缺陷、焊缝缺陷试件进行检测试验。检测试验结果表明:检测速度增大后,管体类裂纹阻抗图仍具有明显的缺陷线形特征(如下图),环焊缝类裂纹阻抗图也具有明显的缺陷、焊缝线形特征(如下图),说明可以在高速状态下获取缺陷的检测信号。
不同速度下缺陷深度为50%wt的环焊缝类裂纹阻抗对比图
·提离值对检测信号的影响
为了分析提离值对涡流检测信号的影响,选取不同的提离值对80%wt缺陷深度的类裂纹试件进行检测试验。检测试验结果表明:随着探头提离值增大,管体类裂纹、环焊缝类裂纹阻抗实部与虚部的峰值(如下图)均明显减小,且环焊缝类裂纹的阻抗幅值受提离值影响阻抗幅值,其衰减速度略快。当提离值过大时,由于阻抗峰值较小,无法准确区分缺陷的信号特征,且环焊缝处形貌不规则。为了准确地识别缺陷的涡流信号,应尽量贴近管道表面或选择较小的提离值进行缺陷检测,避免缺陷漏检。
不同提离值下管体类裂纹阻抗对比图
不同提离值下环焊缝类裂纹阻抗对比图
结束语
针对油气管道类裂纹缺陷的内检测技术难题,自主搭建了高速自动涡流检测试验装置,加工制作了不同尺寸的类裂纹缺陷,通过开展类裂纹缺陷涡流自动检测试验,从信号可识别性、缺陷深度、检测速度、提离值、信噪比等不同角度验证了电磁涡流技术应用于管道类裂纹缺陷内检测的可行性。电磁涡流技术可以实现内检测工况下类裂纹缺陷的检测与识别,为后续开展电磁涡流内检测技术的系统应用、内检测器的研发奠定了良好的基础。
陕西中科非开挖技术股份有限公司是一家能够为建设管理部门、管道业主、管道设计院提供非开挖管道技术咨询、研发、设计、建设等集成服务的企业。主营业务: ◎长距离水平定向钻地质勘察、隧道排导水◎非开挖管道敷设◎非开挖管道检测、修复、更换◎非开挖顶管施工
联系电话:15291453547 网址:http://www.zkpipe.com/
素材来源于网络,如有侵权请联系删除。
网址:www.zkpipe.com
扫码微信直接咨询
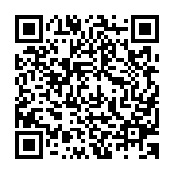